APS系统通过构建产供销计划协同平台帮助航空航天业的客户提高了生产计划的制定效率和准确性,增强了企业对市场变化的适应能力,是企业进行数字化生产不可或缺的重要工具。
航天航空解决方案
航空航天行业数字化转型面临巨大挑战
航空航天行业是一个高度复杂和技术密集的领域,它包括设计、制造、测试和维护飞机、航天器、导弹、卫星以及其他相关设备和系统。航空航天产品具有高度的安全性、可靠性和性能要求,因此对技术和质量控制有着极高的标准。而行业所存在的高度定制化产品、长周期供货和复杂的供应链,对生产计划的有效性提出了相当高的要求。

资源冲突难平衡
以人工维护及人工决策为主,难以统筹考虑资源产能,缺少对计划系统性排产,资源系统性调动,生产现场临时调配,顾此失彼的情况时有发生。

年度/季度策划难
年度策划对资源认识不到位,没有科学的分析出产量与资源的匹配度,导致批产与研制资源冲突严重,年度策划不能科学指导月度生产安排。

外协需求无法合理分配
外协、自制需求分配不能科学的按照资源进行动态调整,难以提前合理安排外协,拉长了整体制造周期,导致企业效能不能充分发挥,制造成本不能有效降低。

计划与物料需求无法联动
生产计划与物料需求计划无法联动,难以快速基于物料变化/计划变更快速联动调整。

工厂/工序联动难
因为各分厂、产线、班组的有限产能都没有数字化建模,各个工序间的产能无法有效衔接,生产执行只能顺水推舟,生产现场临时调配,做一步看一步,顾此失彼的情况时有发生。

生产计划安排无支撑
生产处计划及分厂计划均按照人为经验进行安排,没有生产能力的数据支撑,没有系统性的决策分析辅助,无法进行有限产能的生产计划安排,无法进行计划性工作,导致订单无法按时交货,责任无法追溯。
易普优智能决策解决方案
场景应对方案
需求预测与订单管理
APS系统能够根据市场趋势和历史数据预测需求,同时管理客户订单,确保订单的准确性和及时性。
资源优化
APS通过同步考虑多种有限能力资源的约束,优化包括人力、设备、物料等资源的使用。
物料需求计划
APS能够根据生产计划和BOM(物料清单)准确计算物料需求,进行欠料分析,避免停工待料。
库存优化
实现整个链路的供需平衡,推动各业务功能之间的一致性。确保库存策略更合理。帮助企业将本增效。
交期承诺与订单跟踪
APS能够帮助企业准确答复客户交期,并实时跟踪订单进度,提高客户满意度。
快速排程
APS系统能在短时间内生成详细的生产计划,即使面对大量订单和工序也能迅速响应,支持快速插单和撤单。
工序协同
APS确保工序之间的计划协同,满足前后工艺约束和产能约束,提高生产效率。
产能和负荷分析
APS提供产能负荷分析,帮助企业了解并优化生产能力,减少过度生产或生产不足的情况。
滚动计划
APS支持滚动计划功能,能够根据实时反馈和市场变化动态调整生产计划。
可视化管理
APS系统提供图形化界面,使得生产计划和进度更加直观易懂,便于监控和管理。
算法优化
采用优化算法,如禁忌搜索、模拟退火等启发式算法,以在多重约束条件下找到最优生产计划。
系统集成
自研集成工具实现无缝集成,支撑主流数据库、EXCEL等集成方式,形成完整的系统集成闭环解决方案。
项目亮点
基于国产化要求,提供多级计划仿真推演模块解决方案,规划建设生产计划仿真推演模块及后期的关联项目建设,最终实现基于知识、算法、模型的智能化生产计划排产,基于大数据的计划模型分析、最优策略推荐,基于数字孪生技术,实现虚实融合的计划仿真模拟,分析、验证,打造敏捷的制造体系,为智慧运营决策提供科学、准确、实时的数据支撑。
高效计划
改变了现有的人工计划排产方式,减少了计划制定的工作量,降低了计划沟通的成本,提高计划体系的效率,逐步替代现有的人工线下排产方式。
仿真推演算法底座
构建仿真推演算法底座、车间的数字化排产模型,通过大量的模拟推演试算,评估车间作业各种场景下的工时与产能负荷的表现情况,梳理现场业务、场景涉及到的动态/静态排产约束条件,为计划提供准确的约束支撑,计划具体到每道工序,每台设备,计划开工/完工时间精确到天。
标注化管理流程
将现有计划模式通过计划仿真推演模块实现将线下的操作过程转换为线上系统标准化流程,以生产为主线拉动整个车间的生产协同高效作业,构建面向项目交付的一体化生产计划体系,自动/半自动排程推演,减少因人工排产带来的资源不均衡、精准度差等问题,保障正常的平稳性,行成可执行性更强的计划方案。
工厂/工序协同
通过项目建设,推动厂内策划评估、厂级/分厂级生产能力的数字化能力建设,使得资源、物料等生产资源配置持续优化,达到以计划管理为岗驱动生产业务水平提升的目的,并以此为契机,以问题为导向驱动主价值链条数字化水平提升。
成功案例
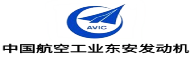